最新消息 / NEWS
2023-11-14 【壓力成型】醫療器材公司Oertli如何在24小時內使用壓力成型製作醫療包裝原型
【壓力成型】醫療器材公司Oertli如何在24小時內使用壓力成型製作醫療包裝原型
近年來,硬體製造商首次發現,外包和死守僵化的原型製作流程既會帶來正面的影響,也會帶來消極的後果。因此,許多製造商轉向桌面製造,以重新控制需要最大靈活性的關鍵零件設計。
Malte Heuer 是 Oertli Instrumente AG 公司的開發工程師兼產品經理。公司總部位於聖加侖萊茵河谷,在那裡專門生產用於眼科手術的高質量手術器械和醫療器械,並在該地區獨家開發和製造其產品,以確保瑞士品質、精度和可靠性。
Malte向研發和工程部門介紹了Mayku Multiplier及其壓力成型技術。通過採用桌面壓力成型技術,Oertli 展示了內部敏捷原型設計可以顯著提高效率和產出質量。
( 相關文章 : 【熱成型應用】真空成型V.S.壓力成型,差別在哪?一次告訴你! )
CathaRhex 3(來源:Oertli )
Oertli 研發機構內部擁有廣泛的製造技術,包括樹脂3D列印、FDM 3D列印和其他原型製造設備。利用這些不斷擴展的技術,公司每天都能以更快的速度進行設計、測試和叠代,從而獲得競爭優勢。
Oertli 研發機構的桌面 3D 列印設備(來源:Oertli )
從挫折到創新
盡管Oertli 在可持續發展、創新實力和設備改進方面進行了大量投資,但硬體開發仍面臨一些挑戰。直到最近,醫療設備包裝仍是挑戰之一。
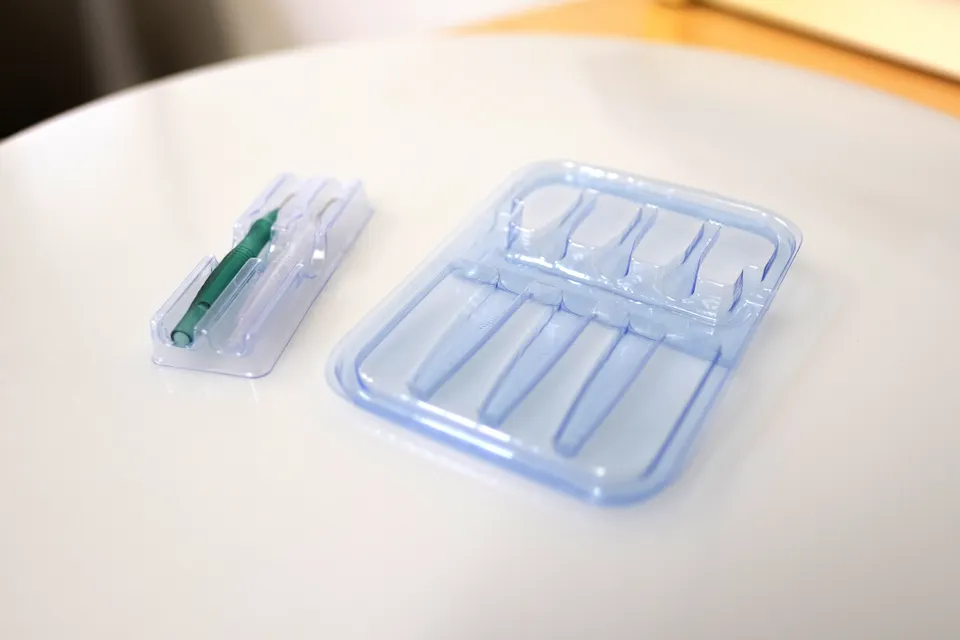
使用Mayku Mutiplier 壓力成形機製作的醫療包裝原型(來源:Oertli )
在Oertli 內部,通常的包裝原型製作過程非常緩慢,需要將原型製作外包給最終的熱成型包裝供應商,每輪設計叠代需要 3 周時間,每個包裝組件需要 2-6 輪設計。
研發團隊將設計包裝,並使用 FDM 3D 列印技術製造有限的視覺原型。這個原型不具備任何功能,因為用於固定組件的包裝下凹槽不夠靈活使壁厚減小,任何 3D 列印技術都無法列印出功能性的原型。
一旦得到產品管理團隊的批准,設計將發送給包裝供應商,後者將在約三週內製作原型。功能性原型然後被運送回來,由客戶進行測試,並收集反饋。這個過程將重複,直到找到完美的設計。
將智慧方法引入製造
這種設計叠代過程效率低下,因此當 Malte 負責醫療包裝原型設計時,他將自己的 SCRUM Master 技能付諸實踐,尋找一種能讓原型設計更加快速的技術。在Google上搜尋桌面型但功能強大的熱成型機時,他發現了 Multiplier,並迅速看到了其在Oertli內的潛力並購買了它。
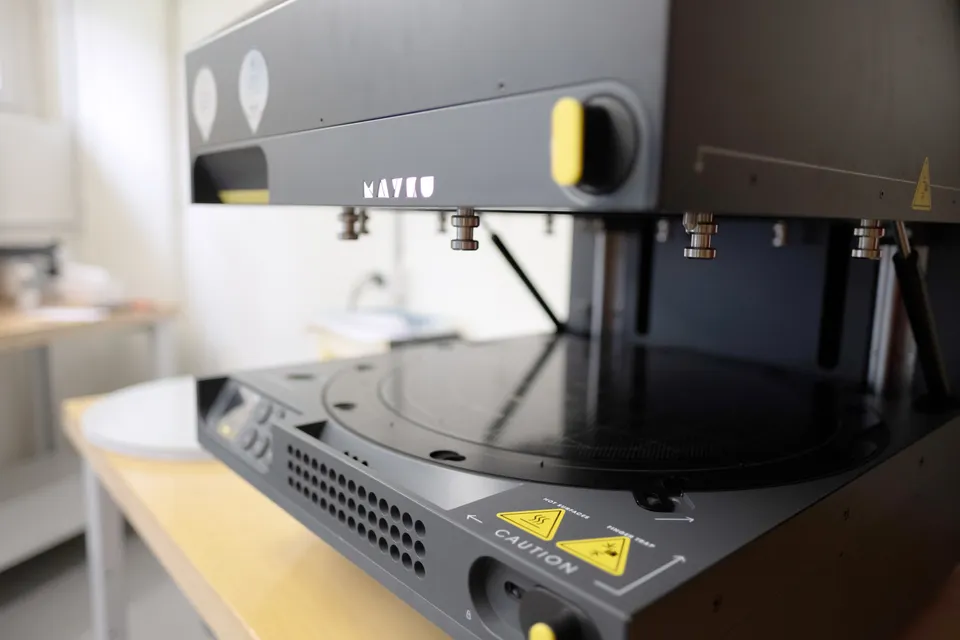
歐特力研發設施中的 Mayku Multiplier(來源:歐特力)
Malte能夠輕鬆地將Multiplier整合到現有的原型製作工作流程中,保留已經高效的關鍵環節,並優化造成問題的環節。他仍然使用 Solidworks 設計包裝原型。不過他不再使用 3D 列印可視化原型來提交給產品管理團隊、外包給包裝供應商,而是使用 3D 列印設計的熱成型模板 ( 相關教學 : 【壓力成型】新手一定要知道的12個熱成型設計原則 )。然後,他使用 Multiplier 創造 3-10 個高保真原型,並提交給團隊和測試人員。所有這些都可以在一天內完成。
『如果產品管理在會議中提出一個小的變更,以前需要三週才能實施並安排更新會議。現在可以在一天內進行變更,並安排次日的會議,每個人都記得昨天會議的細節。』- Malte Heuer - Oertli Instrumente AG 開發工程師兼產品經理
由於高保真原型的要求,Malte 決定使用像 Mayku Multiplier 這樣的壓力成型機。評估設計需要 +-0.1 毫米的公差,而真空成型等其他技術無法達到這種精度。
內部壓力成型的投資回報率
將高保真原型設計引入公司內部,使Oertli 得以保持創新和敏捷。他們幾乎可以在第一時間對工程需求和團隊反饋做出響應,而不會出現典型硬體製造商在製作原型時所面臨的任何浪費或低效問題。
『從軟體開始的快速循環時間,現在已延伸到整個機械部門。』- Malte Heuer - Oertli Instrumente AG 開發工程師兼產品經理
通過使用 Multiplier,Oertli 將設計叠代周期從三周縮短到一天。他們還將原型設計周期的成本降低了 90% 以上,同時仍能做出高保真度的原型。他們現在可以在公司內部製作原型,從而能夠完全控制整個流程。
參考原文